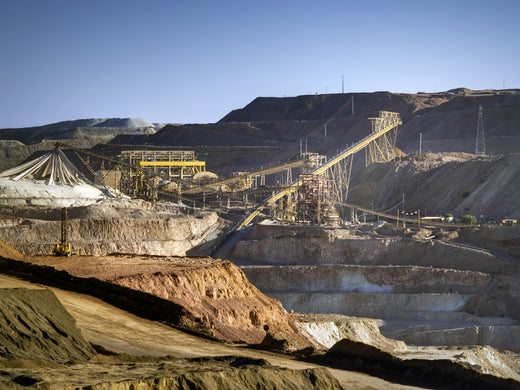
Improve mega projects by using an integrated systems approach
Rob RitchieBuilding industrial mega projects requires a complex set of interrelated processes. They often concurrently bring together elements of engineering design, procurement of equipment, materials, and services to the field. Traditionally, these projects have had a poor track record of meeting schedule and budget estimates, with overruns being commonplace. Worse is that the performance of delivery for these projects is, effectively, going backward.
Mega projects are enormous, highly complex projects that establish industrial plants and facilities. They are categorised as mega projects when the overall investment is over $1bn. Their complexity usually comes from the scale of the project and the need to satisfy a large number of stakeholders.
The overall complexity of these projects is usually complicated by the number of different organisations that come together during a project. Often there is a lack of cohesion in how these organisations jointly manage the planning, task allocation, shared equipment, material requirements, and logistics to support the mobilisation of people, assets and materials.
Ultimately, difficulty in planning manifests as poor labour utilisation in the field. A study by COAA has found that tradesmen spend only 37% of their time working on the tools, with 29% of their time spent waiting for materials or leaving early with an inability to complete work.
Ironically, stagnant performance on these projects has occurred when the industry has made significant investments into methods and technologies to support productivity improvements. This has included the introduction and widespread use of 3D modelling, and Building Information Modelling (BIM) initiatives increasingly becoming the norm.
Projects often fail to adequately invest in their own productivity or fail to understand how to deliver results from that investment. In an urgent rush to move towards a schedule, siloed work practices are commonplace. Project teams fail to adequately map their work processes, take the time to implement the supporting technology and instead, they still rely on manual processes as a method of expediency. These tactics almost always fail. Silos become the bottlenecks that crush productivity across the supply chain.
Well implemented and integrated technology for a mega project requires taking a total supply chain perspective. Systems and data exchange of the entire supply chain need to be pieced together as a holistic system, not individual parts. BIM standards like PAS 1192-2 describe the management of information across the supply chain. Using these standards with integrated business processes (e.g. the COOA promoted Advanced Work Packaging) can create the foundation for significantly improved productivity on mega projects.
The rush to begin execution on the project can destroy any hopes of effectively embedding work practices that incorporate an integrated systems approach into the project. Implementing systems early is a critical success factor in their potential to deliver any anticipated benefits. The Cravern Group specialises in helping our clients take an integrated systems approach to mega project implementation.